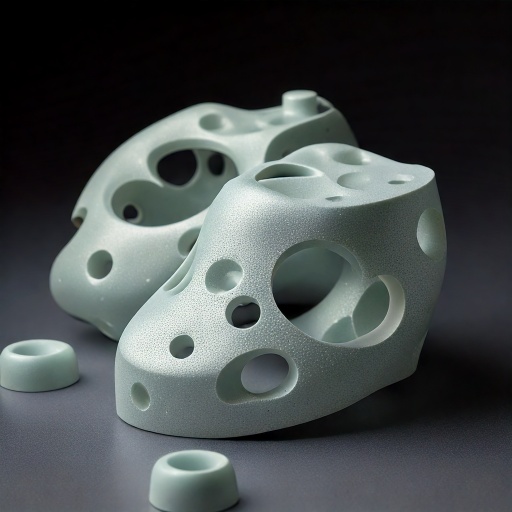
Custom Parts with Superior Flexibility & Durability
At NetProto, our urethane casting services offer a versatile, cost-effective solution for producing high-quality prototypes and low-volume production parts. Whether for functional testing or end-use applications, we deliver precision-crafted parts tailored to your exact specifications.
What is Urethane Casting?
Urethane casting is a manufacturing process that uses silicone molds to produce high-quality, low-volume plastic parts. This process is ideal for creating parts with complex geometries, smooth finishes, and flexible or rigid material properties.
The process begins with a master pattern, typically created via 3D printing or CNC machining, which is used to form a silicone mold. The mold is then used to cast urethane resins, creating parts with exceptional detail and quality.
Benefits of Urethane Casting
Urethane casting combines efficiency, flexibility, and quality, making it a preferred choice for many industries:
- Low-Volume Production: Perfect for short-run manufacturing and bridge production.
- Cost-Effective: Lower tooling costs compared to injection molding.
- High-Quality Finishes: Achieves smooth, detailed parts with a variety of textures and finishes.
- Material Versatility: Offers flexible, rigid, or elastomeric properties.
- Fast Turnaround: Short lead times for prototypes and production.
Applications of Urethane Casting
Urethane casting is widely used across industries for a range of applications, including:
- Automotive: Perfect for short-run manufacturing and bridge production.
- Medical Devices: Lower tooling costs compared to injection molding.
- Consumer Products: Achieves smooth, detailed parts with a variety of textures and finishes.
- Industrial Equipment: Offers flexible, rigid, or elastomeric properties.
- Electronics: Short lead times for prototypes and production.
Our Urethane Casting Capabilities
- Master Pattern Creation
- We use high-precision 3D printing or CNC machining to create detailed master patterns, ensuring accurate silicone molds.
- Silicone Mold Fabrication
- Our expert technicians produce high-quality silicone molds that capture every detail of your master pattern.
- Material Options
- Choose from a wide variety of urethane resins to meet your specific needs, including:
- Flexible materials for soft-touch parts.
- Rigid materials for durable components.
- Transparent or color-matched materials.
- Choose from a wide variety of urethane resins to meet your specific needs, including:
- Surface Finishing
- Achieve custom textures, polished finishes, or matte surfaces to meet your design and aesthetic goals.
Urethane Casting Design Considerations
To optimize the urethane casting process, consider the following design guidelines:
- Wall Thickness
- Maintain consistent wall thickness to reduce warping and ensure uniform curing.
- Draft Angles
- Apply draft angles for smooth removal from silicone molds.
- Undercuts
- Avoid deep undercuts, or design parts with removable sections in the mold.
- Material Selection
- Choose materials that match your functional and aesthetic requirements, including flexibility, durability, and transparency.
Why Choose NetProto for Urethane Casting?
Custom Solutions: Tailored to your specifications, ensuring the perfect fit for your project.
Fast Turnarounds: Get prototypes and short-run production parts in days, not weeks.
Material Expertise: Access to a wide range of urethane materials for unique applications.
High-Quality Finishes: Achieve exceptional surface detail and aesthetics with our advanced techniques.
Cost-Effective Prototyping: Avoid expensive tooling with affordable silicone molds.
How Urethane Casting Works
1. Master Pattern Creation
– A high-precision master pattern is created via 3D printing or CNC machining.
2. Silicone Mold Fabrication
– A silicone mold is formed around the master pattern, capturing every detail.
3. Urethane Casting
– Urethane resin is poured into the mold, cured, and removed to create the finished part.
4. Post-Processing
– Parts are deburred, polished, or textured to meet your specifications.
5. Quality Inspection
– Each part undergoes rigorous inspection to ensure consistency and performance.
Start Your Urethane Casting Project Today