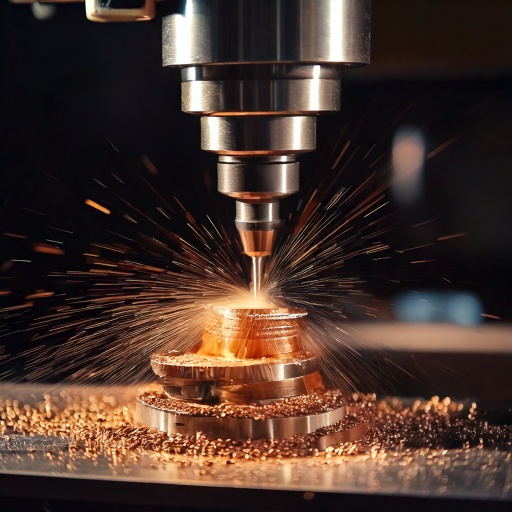

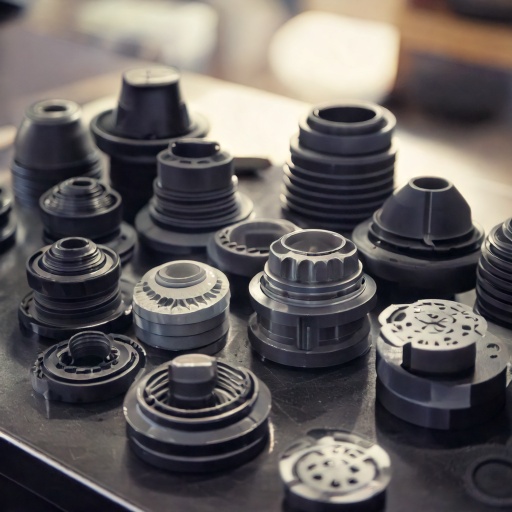
Why Choose NetProto for CNC Machining?
Advanced Technology: State-of-the-art equipment ensures precision and efficiency.
Expert Engineering Support: Our team guides to optimize your designs for CNC machining.
Fast Lead Times: Rapid prototyping and production to meet tight schedules.
Comprehensive Quality Control: Every part undergoes rigorous inspection to guarantee consistent quality.
Global Delivery: Flexible shipping options for regional and international projects.
Wall Thickness
Maintain a minimum wall thickness of 0.8mm for metals and 1.5mm for plastics to avoid warping or structural issues.
Tolerances
Specify tolerances only for critical features to reduce machining costs. Standard tolerances of ±0.005” work well for most applications.
Internal Radii
Use a minimum internal corner radius of 1/3 the cavity depth to accommodate tool geometry and reduce stress concentrations.
Hole Sizes
Design holes to standard drill bit sizes for faster production and cost savings.
Undercuts
Minimize or avoid undercuts to simplify tool paths and reduce production complexity.
Threads
For threaded features, design threads with standard dimensions, such as M6 or ¼-20.
Part Complexity
For intricate parts, consider multi-axis CNC machining (3, 4, or 5-axis) to achieve the desired geometry.
Surface Finishes
Specify finishing needs such as polishing, bead blasting, or anodizing to achieve the desired look and performance.
Tool Clearance
Ensure there is enough clearance for tools to access all features without interference.
Material Selection
Choose materials based on the application’s requirements for strength, durability, and thermal or chemical resistance.